A converted coal to gas gravity heat furnace with a Honeywell V155 gas valve that sticks open. The slightest vibration releases it.
↧
V155 sticking
↧
New Yorker CG D Gas Boiler
I have a New Yorker CG D gas boiler. Installed by a licensed plumber and works great. recently an engineer inspected my house and noted that my base clearance was insufficient. He said I needed 18 inches clearance from the floor at the base of the unit. How is that possible? My unit sits on 4 inch blocks and works fine. Is he correct?
↧
↧
Output of Burnham Baseray below 150F?
Hi all,
Could someone point me to a resource that will give me some sense of the output of Baseray cast-iron baseboard in low-temperature systems? The spec sheet doesn't go below 150F, and I suspect at some point it's non-linear.
Background: I'm a homeowner in the Boston area and have a Buderus GB142 hooked up to a high-mass radiators (circa 1912; the system originally ran on gravity), using a Tekmar unit for outdoor reset, and even on the coldest days of the year, we don't see water temps above the 140s. It's about 40 outside today, and the system is calling for a temp around 100F (the boiler actually thinks it is hooked up to low-mass radiant). The system is comfortable and very efficient.
Background: During a previous renovation, Buderus panels were installed (on PEX) in the bathroom and kitchen. I'd like to relocate them to a separate (currently unconnected) basement zone, because we've found that at low temps, they simply don't put out much heat and they are located in areas where I'd like to put other things. If the bathroom panel gets obstructed by a towel, the output drops even further.
We are renovating and the additional sealing and insulating may help, but I'm still interested in CI baseboard because it would take less space and I'm guessing that CI baseboard would match up better with the rest of the main zone. (We unfortunately don't have the room to restore the original radiators).
I'm working with a plumber our GC is using for the rest of the job, and it would be great to get a sense of the output in the 105-125 range and how that matches up with the heat loss before going forward, and whether others have had success with similar arrangements.
Thank you!
Could someone point me to a resource that will give me some sense of the output of Baseray cast-iron baseboard in low-temperature systems? The spec sheet doesn't go below 150F, and I suspect at some point it's non-linear.
Background: I'm a homeowner in the Boston area and have a Buderus GB142 hooked up to a high-mass radiators (circa 1912; the system originally ran on gravity), using a Tekmar unit for outdoor reset, and even on the coldest days of the year, we don't see water temps above the 140s. It's about 40 outside today, and the system is calling for a temp around 100F (the boiler actually thinks it is hooked up to low-mass radiant). The system is comfortable and very efficient.
Background: During a previous renovation, Buderus panels were installed (on PEX) in the bathroom and kitchen. I'd like to relocate them to a separate (currently unconnected) basement zone, because we've found that at low temps, they simply don't put out much heat and they are located in areas where I'd like to put other things. If the bathroom panel gets obstructed by a towel, the output drops even further.
We are renovating and the additional sealing and insulating may help, but I'm still interested in CI baseboard because it would take less space and I'm guessing that CI baseboard would match up better with the rest of the main zone. (We unfortunately don't have the room to restore the original radiators).
I'm working with a plumber our GC is using for the rest of the job, and it would be great to get a sense of the output in the 105-125 range and how that matches up with the heat loss before going forward, and whether others have had success with similar arrangements.
Thank you!
↧
Viessmann Vitodens 200 6-24C code 06
Need help as Viessmann tech support is now closed for the weekend and I have cold irritated customers.
During a cold spell about 2 weeks ago now boiler shut down with a code 06 and red fault light but would randomly also display a 07 and FE when reset. I checked all the venting for possible ice build-up or other blockage but it was clear. After talking with tech support they thought the LGM board was burned out due to the randomness of the errors so I replaced that and it now consistently displays code 06 and no red fault light. After second call to tech they suggested I verify blower function by pulling the high limit wire, I did that and no blower which felt quite hot to the touch. I just replaced the blower this afternoon but still code 06. I am able to clear the error and it stays clear but no start-up sequence. Now when I pull the high limit wire blower does start so I'm pretty confident both board & blower were toast but what would you recommend the next step be?
During a cold spell about 2 weeks ago now boiler shut down with a code 06 and red fault light but would randomly also display a 07 and FE when reset. I checked all the venting for possible ice build-up or other blockage but it was clear. After talking with tech support they thought the LGM board was burned out due to the randomness of the errors so I replaced that and it now consistently displays code 06 and no red fault light. After second call to tech they suggested I verify blower function by pulling the high limit wire, I did that and no blower which felt quite hot to the touch. I just replaced the blower this afternoon but still code 06. I am able to clear the error and it stays clear but no start-up sequence. Now when I pull the high limit wire blower does start so I'm pretty confident both board & blower were toast but what would you recommend the next step be?
↧
Navien NCB 240 flame loss (error 12)
Hi all,
A couple times a day, and especially every early morning, I get Error 012 (flame loss) at my Navien NCB 240. I have to reset the boiler to make it work again. I have called the installer multiple times but the problem persists. Here is what I have done so far. All with installer and recommendations of Navien support hotline:
- usual maintenance with cleaning filters etc.
- replacement of ignition rod
- redid my entire chimney with brand new polypropylene exhaust and fresh air intake
The boiler was manufactured in 2013 and installed in 2014. It used to run without problems for a while and started to cause problems the last few months, although nothing was changed.
I hope to find someone who has some new ideas or who heard of a similar problem?
Thanks, I am at the point of desperation and am thinking of having to replace this brand new boiler.
A couple times a day, and especially every early morning, I get Error 012 (flame loss) at my Navien NCB 240. I have to reset the boiler to make it work again. I have called the installer multiple times but the problem persists. Here is what I have done so far. All with installer and recommendations of Navien support hotline:
- usual maintenance with cleaning filters etc.
- replacement of ignition rod
- redid my entire chimney with brand new polypropylene exhaust and fresh air intake
The boiler was manufactured in 2013 and installed in 2014. It used to run without problems for a while and started to cause problems the last few months, although nothing was changed.
I hope to find someone who has some new ideas or who heard of a similar problem?
Thanks, I am at the point of desperation and am thinking of having to replace this brand new boiler.
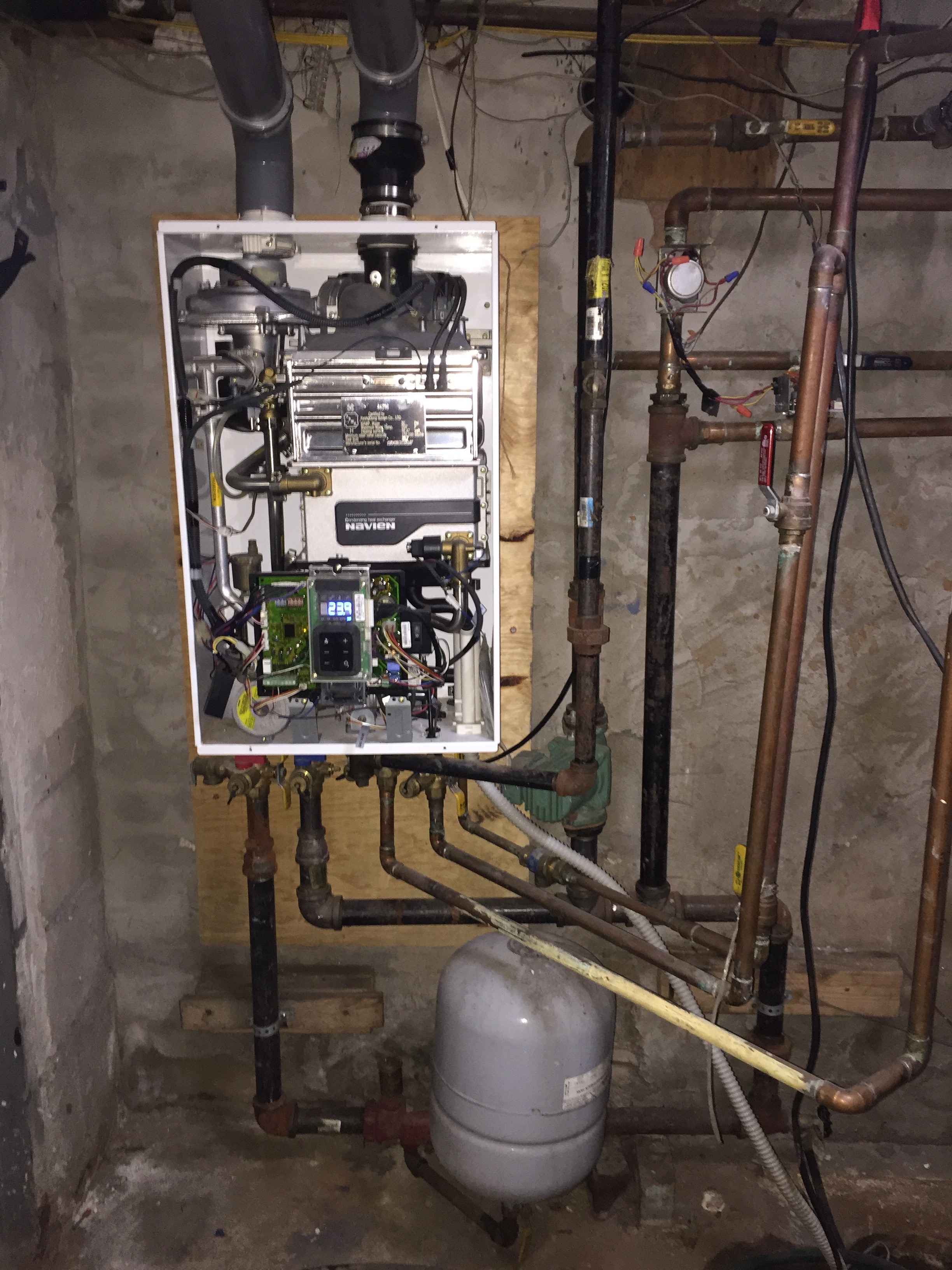
↧
↧
Vent size reduction from appliances to connector and chimney liner
Hi everyone,
I'm a 1st time homeowner and my chimney recently needed to be relined (blockage had caused boiler to turn off).
We have 2 appliances - a 40K BTU Water Heater and a 187K BTU Boiler. The boiler has a 7" exhaust and the water tank has a 4" exhaust. The Chimney height is 35-40 ft.
The chimney guy that came installed a double walled 5.5" smoothwall flex stainless steel chimney liner. He also installed a 6 inch connector coming off the boiler (reduced from 7" exhaust), and again reduced at the chimney liner to 5.5".
He insists that he's been in the business for over 20 years and everything was done correctly.
Anyone have experience with this?
Thank you in advance!
I'm a 1st time homeowner and my chimney recently needed to be relined (blockage had caused boiler to turn off).
We have 2 appliances - a 40K BTU Water Heater and a 187K BTU Boiler. The boiler has a 7" exhaust and the water tank has a 4" exhaust. The Chimney height is 35-40 ft.
The chimney guy that came installed a double walled 5.5" smoothwall flex stainless steel chimney liner. He also installed a 6 inch connector coming off the boiler (reduced from 7" exhaust), and again reduced at the chimney liner to 5.5".
He insists that he's been in the business for over 20 years and everything was done correctly.
Anyone have experience with this?
Thank you in advance!
↧
Turning on zone valve manually
(long story - hopefully short) ... I'm trying to confirm where my current issue is with getting no heat to 1 of 2 baseboard heat zones. I've been spending days working on thermostat wiring and have been told I have it correct, but I'm not confident in that. Currently - I have both zones calling for heat. Zone1 - works fine (always has); Zone2 (that I've been trying to fix) ... gets no heat. I'm hoping to confirm my issue is back with the thermostat wiring directly to the zone valve - so I've manually opened the zone valve ... and expect I should get baseboard heat in both zones. This is my second attempt at this ... I didn't get any heat yesterday when I tried this (it was late - I'm hoping I was half asleep or something). And I'm not sure how long it should take for the heat to get upstairs. Am I on the right track?
↧
ECOBEE t-stat wiring
I'm weeks into this open issue ... can anyone provide a recommendation? I have two t-stats. 1 handles 1 heating zone and my AC and I've installed an ECOBEE3 WIFI t-stat there and everything has been perfect. On my second zone (boiler heat only) ... I've attempted to install a second ECOBEE3. I don't have a common wire ... so included in the wiring is the addition of a FAST-STAT unit. I've been in numerous contacts with ECOBEE help desk and even called FAST-STAT -- but I can't get the zone value to work (I have manually confirmed that the heat works on the zone valve). I can't get ECOBEE support and FAST-STAT to agree with where the FAST-STAT should be wired (one says at the zone value - the other at the boiler). I've tried both ... neither have worked. I have a Honeywell circulator board with TV, T, W and Z wiring ports. And I have TACO zone values with 3 wiring connections. Can anyone provide guidance on how to connect the FAST-STAT receiver at the boiler/zone valve side (the sender at the t-stat appears to be straight forward).
↧
Anyone using this HTP ETF Combi boiler
Anyone using this boiler
High Efficency
EFT COMBI
Wall Mount
Tankless Water Heater & Space Heating Appliance
140K & 199K Btuh Units
Pros and cons please
Thanks
High Efficency
EFT COMBI
Wall Mount
Tankless Water Heater & Space Heating Appliance
140K & 199K Btuh Units
Pros and cons please
Thanks
↧
↧
Duct furnace needed
Does anyone know of a company that make a gas fired duct furnace between 125- 150 mbh input, that is now more wide then 21"? We need to replace a modine duct furnace that was installed in the building before the roof was installed. Now the heat exchanger is cracked, and the heater needs to be replaced. The only way to get the new heater in the attic is through the access hole which 41"x21"
Thanks to all
Thanks to all
↧
Boiler Stops Heating Periodically, Power Reset Fixes It
My boiler stops heating periodically and I'd appreciate some insight on how to address it.
I've got a 3 year old Weil-McLain GV90+ 3 Series 2 boiler. Single zone plus indirect water heat. Taco circulators.
Periodically, like every couple months, our boiler stops making hot water. Thermostat and indirect water heater put in calls at the zone valve, but boiler doesn't respond. Cycling the breaker or the switch at the boiler make everything good as new, until it happens again. I've done the checklist in my manual:
- the breaker isn't tripped
- I don't get 120 VAC across my circulator pins
- I don't have any red lights and the system isn't in lockout
- There is no obvious signs of trouble, though the relief valve is weeping slightly
- The toubleshooting guide concludes to replace the controller board
Any thoughts? It seems that the controller replacement is simple enough for a DIYer, but I'd like to be sure that it is the cause. Thanks.
I've got a 3 year old Weil-McLain GV90+ 3 Series 2 boiler. Single zone plus indirect water heat. Taco circulators.
Periodically, like every couple months, our boiler stops making hot water. Thermostat and indirect water heater put in calls at the zone valve, but boiler doesn't respond. Cycling the breaker or the switch at the boiler make everything good as new, until it happens again. I've done the checklist in my manual:
- the breaker isn't tripped
- I don't get 120 VAC across my circulator pins
- I don't have any red lights and the system isn't in lockout
- There is no obvious signs of trouble, though the relief valve is weeping slightly
- The toubleshooting guide concludes to replace the controller board
Any thoughts? It seems that the controller replacement is simple enough for a DIYer, but I'd like to be sure that it is the cause. Thanks.
↧
Boiler temp too high? Causing loud banging?
I have a Lochnivar plus Knight wall mount boiler control module. It provides hot water to two hydronic radiant floor loops and the exchanger in the domestic hot water tank. It was working well for the first couple of years. Now the only defect is this: for a couple of years it is making loud explosive bangs at moments I can't predict. I recently sat next to it for 5 hours waiting in vain for a bang so I could see what the control screen said. Within a day it made 3 or 4 bangs in a half hour stretch while I was elsewhere in the house.
I called in the installing business but found out my installer was no longer working there, and the new person seemed to find nothing wrong. That business is not functioning any longer. I have the service manual, but of course user access to the settings is almost nonexistent; it allows only installer access.
Banging like that feels like something too hot encountering cold. This phenomenon is way worse in winter. What should I do?
I called in the installing business but found out my installer was no longer working there, and the new person seemed to find nothing wrong. That business is not functioning any longer. I have the service manual, but of course user access to the settings is almost nonexistent; it allows only installer access.
Banging like that feels like something too hot encountering cold. This phenomenon is way worse in winter. What should I do?
↧
Rinnai combi E110C
For the past 4 weeks my own Combi will deliver a sudden momentary cold blast of cold water while in the shower. Lasts for maybe 1 minute then hot again and good, not fun! Can't figure it out doesn't seem to have loss of gas or water pressure. Not sure if it is through out the house or just this shower. Might check the shower valve but I doubt that is the problem. Clean the boiler with vinegar yearly. Crazy.
↧
↧
Source for Burnham ES2 orifices?
I am about ready to have a Burnham ES25 CI boiler installed. The ES25 is 2 weeks out since I need the LP version. I can get the NG one now but the LP conversion kit (gas valve and orifices) is also 2 weeks out. So I tracked down the gas valve and all I need are 8 orifices. They're 1.2mm (3/64" or #56). I don't know anything else about them such as their thread size, etc. I could drill out something that's smaller if I could find them.
Is this a semi-standard part that can be cross-referenced and sourced somewhere else? The Burnham part number is 822792 but that's just for the 1.2mm. I don't have part numbers for anything else that physical size that could be drilled out.
Current system is working so not an emergency but I will run into travel conflicts if I have to wait 2 weeks. Plus the chimney liner installer has a huge stack of scaffolding on my chimney that has to stay until the boiler install - so would like to move forward if possible.
Is this a semi-standard part that can be cross-referenced and sourced somewhere else? The Burnham part number is 822792 but that's just for the 1.2mm. I don't have part numbers for anything else that physical size that could be drilled out.
Current system is working so not an emergency but I will run into travel conflicts if I have to wait 2 weeks. Plus the chimney liner installer has a huge stack of scaffolding on my chimney that has to stay until the boiler install - so would like to move forward if possible.
↧
How to trouble shoot circulation issues for a hot water boiler
I have a residential crown cxe 5 boiler with a grundfos type up pump. I am getting inconsistent heating. I suspect that there is a circulation problem because when a thermostat calls for heat, the boiler comes on, but shuts off prematurely. On shut-off, the water temp is about 200 F, which I think is the limit temperature. The pump and pipes sometimes feel like water is circulating and sometimes not. How do I remove the cover plate on the pump to see it it is turning? Any other thing to check would also be appreciated. Thanks
↧
Heat exchanger location
Can anyone tell me where the heat exchanger is located on my Axia 29E?
↧
Ignition Control for Weil Mclain: M# EG1PEG-35, Series 4
Hello, anyone know of a Universal control for the Weil Mclain: M# EG1PEG-35, Series 4? We ordered the OEM part Thursday from a larger regional vendor and they shipped it to Maine (and yes we got a part that was supposed to go to some contractor in Maine). UPS shows up Friday with the wrong part.
Thanks, Gary
Thanks, Gary
↧
↧
Pressure relief valve leaks after zone valve install
I have a Burnham series 2 boiler where the pressure relief valves seems to start leaking after turn the thermostat off or it reaches itso temptress. I checked the expansion tank pressure 15psi , boiler off pressure is 15 psi aswell. I've shut the thermostat off and watched the pressure climb to 30 psi and start dripping. This is after adding baseboard heat and zone valves to my basement. Any ideas? Thanks!
↧
Cast Iron Oil Boiler to ModCon LP, 2.5x fuel usage increase
Recently converted from a 25+ year old cast iron oil boiler (last checked was operating at 78% efficiency) with separate oil fired hot water tank to a Navien NHB-80 with indirect hot water tank.
Last December on old boiler we used about 100 gallons of oil, this December we used about 250 gallons of LP (2000sqft log house with quite a bit of glass). The propane usage seems a bit out of control and I have no faith in the company that installed the new system.
The one big change we did make is with the oil boiler we set the heat back to 62 at night and during the day, with the new system we keep the heat at a constant 68. All of the reading I did has pointed towards set backs with a mod con are counter productive (even though we would prefer the colder temps at night...).
Aside from short cycling, what else would be the cause of the big increase in fuel usage? I have the heating people coming in on Friday to take a look and would like to be able to provide them as much direction as possible as.
Also, if anyone knows any experienced technicians in the Albany, NY area, please let me know!
Last December on old boiler we used about 100 gallons of oil, this December we used about 250 gallons of LP (2000sqft log house with quite a bit of glass). The propane usage seems a bit out of control and I have no faith in the company that installed the new system.
The one big change we did make is with the oil boiler we set the heat back to 62 at night and during the day, with the new system we keep the heat at a constant 68. All of the reading I did has pointed towards set backs with a mod con are counter productive (even though we would prefer the colder temps at night...).
Aside from short cycling, what else would be the cause of the big increase in fuel usage? I have the heating people coming in on Friday to take a look and would like to be able to provide them as much direction as possible as.
Also, if anyone knows any experienced technicians in the Albany, NY area, please let me know!
↧
Flow control
Installed a Navien 180 combi. 1 zone fine HW fine but the other zone no flow. T stat calling red light on on TAco SR 502 calling for heat. Circ was on when I left the job heat coming up good. Customer calls no heat. No blown fuses on taco board. I am suspicious about the IFC little plastic flow checks you put inside circs. Just started using them wondering if this is the problem. Could be air although I bled good. Anybody have problems with these types of flow checks? THX
↧