As a prelude to a possible mod-con installation, I have been studying up on some of the Caleffi and Taco videos which are really helpful so that I can clearly see that it will work. According to TACO and others, usually the head sizing formula provides safety at the high-end but often oversizes the pump, but if the required flow rate is within the pump curve then it works. The chat on heat forums seems to suggest that there aren’t enough small ECM circulators out there to fit small heating systems––sort of like mod-con boilers.
As I’ve come to understand it, one would want a circulator—whether a zone circulator or a system circulator with zone valves––that is sized so that the expected ‘variable’ service points on the pump curve are well within the circulator’s range. Otherwise it will not in fact serve as a variable speed circulator. It seems to me that using zoning valves means losing some ability to tailor both head and flow to each zone in exchange for energy savings.
I have a three-zone 1800 sq ft house, measured heat loss of 38K, let’s say 40K. Actual heat loss—based on annual heat therms, degree days and 75% old boiler efficiency shows less than 30Kbtu loss. Plan is to use one ECM circ with zone valves.
By estimated method, 3/4" copper pipe measured length of the longest pipe run Zone 2 is 200ft x 1.5 = 300ft x .04 = 12 ft head. I believe this estimate method measures head at 4gpm—which may seem logical as cumulative flow requirements for the 38K loss would be 4gpm @10Kbtu. (In this case the estimated head loss TDL nearly equaled the measured TDL of 308ft.)
By calculated head loss method: TDL 308ft x .015psi/ft for 4gpm Type M copper, design day x 2.31 = 10.67ft head or 12.8 ft head for type L. (See table below.) Pretty close to the estimated method, but again both results are based on 4gpm flow.
So I wanted to check the pump curve to verify that the variable speed TACO Taco-VT2218-HY2-4C1A00 ∆T ECM could handle the lowest flow rate or head loss required when any one or two zones is calling for heat on either a design or shoulder day. The calculated head loss method for that Zone 2—based on the 1gpm it actually requires even on a design day--is much lower: 308ft TDL x .001psi/ft x 2.31 = .711 ft of head Type L or M copper 3/4” copper pipe. So would this circulator handle this zone only on a design or any other day the 0-4gpm at the required water temperature and minimum 2ft-per-second velocity? Or even a three-zone heat call on a non-design day. (see pump curve below.)
(Note that on design day (10ºF), of the three zones, two require only 1gpm and one 2gpm. At 40º OT, total heat loss drops from 38k to 20K, about half, meaning a requirement of only 2gpm flow total for all three zones––0.5gpm for the two smaller zones, 1gpm for larger zone. On the pump curve, 0.5gpm shows about 3.5ft of head pressure, though I know with zone valves gpm is measured cumulatively. So that’s where I’m stuck. If I went strictly circulators instead of zone valves, I’d have to find two ECM circs that each produced about 10K btu on design day at 1gpm and one circ that produced 20K, all zones having 1ft of head based on calculated method.)
Image may be NSFW.
Clik here to view.
Image may be NSFW.
Clik here to view.
As I’ve come to understand it, one would want a circulator—whether a zone circulator or a system circulator with zone valves––that is sized so that the expected ‘variable’ service points on the pump curve are well within the circulator’s range. Otherwise it will not in fact serve as a variable speed circulator. It seems to me that using zoning valves means losing some ability to tailor both head and flow to each zone in exchange for energy savings.
I have a three-zone 1800 sq ft house, measured heat loss of 38K, let’s say 40K. Actual heat loss—based on annual heat therms, degree days and 75% old boiler efficiency shows less than 30Kbtu loss. Plan is to use one ECM circ with zone valves.
By estimated method, 3/4" copper pipe measured length of the longest pipe run Zone 2 is 200ft x 1.5 = 300ft x .04 = 12 ft head. I believe this estimate method measures head at 4gpm—which may seem logical as cumulative flow requirements for the 38K loss would be 4gpm @10Kbtu. (In this case the estimated head loss TDL nearly equaled the measured TDL of 308ft.)
By calculated head loss method: TDL 308ft x .015psi/ft for 4gpm Type M copper, design day x 2.31 = 10.67ft head or 12.8 ft head for type L. (See table below.) Pretty close to the estimated method, but again both results are based on 4gpm flow.
So I wanted to check the pump curve to verify that the variable speed TACO Taco-VT2218-HY2-4C1A00 ∆T ECM could handle the lowest flow rate or head loss required when any one or two zones is calling for heat on either a design or shoulder day. The calculated head loss method for that Zone 2—based on the 1gpm it actually requires even on a design day--is much lower: 308ft TDL x .001psi/ft x 2.31 = .711 ft of head Type L or M copper 3/4” copper pipe. So would this circulator handle this zone only on a design or any other day the 0-4gpm at the required water temperature and minimum 2ft-per-second velocity? Or even a three-zone heat call on a non-design day. (see pump curve below.)
(Note that on design day (10ºF), of the three zones, two require only 1gpm and one 2gpm. At 40º OT, total heat loss drops from 38k to 20K, about half, meaning a requirement of only 2gpm flow total for all three zones––0.5gpm for the two smaller zones, 1gpm for larger zone. On the pump curve, 0.5gpm shows about 3.5ft of head pressure, though I know with zone valves gpm is measured cumulatively. So that’s where I’m stuck. If I went strictly circulators instead of zone valves, I’d have to find two ECM circs that each produced about 10K btu on design day at 1gpm and one circ that produced 20K, all zones having 1ft of head based on calculated method.)
Image may be NSFW.
Clik here to view.
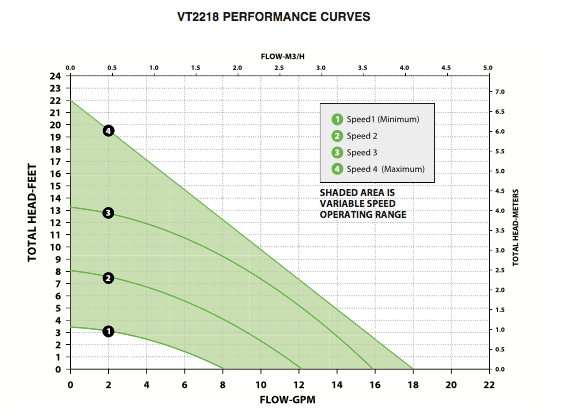
Image may be NSFW.
Clik here to view.
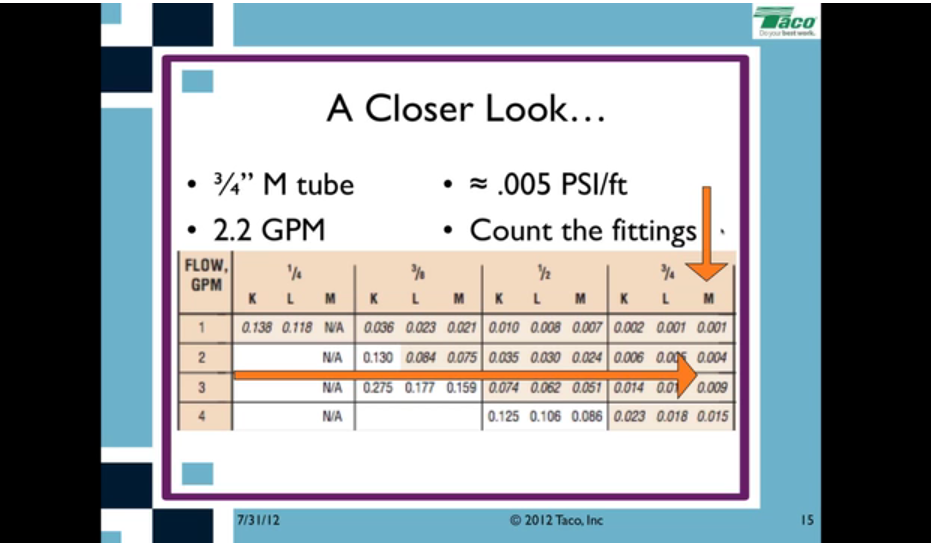